目前新建鍋爐在運(yùn)行前都應(yīng)進(jìn)行化學(xué)清洗,以清除設(shè)備在制造加工過程中形成的高溫氧化軋皮和帶硅氧化皮,以及在存放、運(yùn)輸、安裝過程中所產(chǎn)生的腐蝕產(chǎn)物、焊渣帶入的泥沙、油脂涂層、污染物等。
實踐證明,新建鍋爐如啟動前不進(jìn)行化學(xué)清洗,水、汽系統(tǒng)內(nèi)的各種雜質(zhì)和附著物在鍋爐投運(yùn)后會產(chǎn)生以下危害:
1. 直接妨礙管壁的傳熱或?qū)е滤傅漠a(chǎn)生,使?fàn)t管金屬過熱和損壞,縮短鍋爐的使用壽命。
2. 促使鍋爐在運(yùn)行中發(fā)生沉積物的腐蝕,致使?fàn)t管變薄、穿孔而引起爆管。
3. 在爐水中形成碎片和沉渣,從而引起爐管堵塞或破壞正常的汽、水流動的工藝。
4. 使?fàn)t水的含硅量、含鐵量等水質(zhì)指標(biāo)長期不合格,延長了機(jī)組的啟動時間,危害汽輪機(jī)的正常運(yùn)行。相反,新建鍋爐啟動前進(jìn)行化學(xué)清洗,不僅有利于鍋爐的安全運(yùn)行,還能夠改善鍋爐啟動階段的水汽質(zhì)量,使之較快達(dá)到正常標(biāo)準(zhǔn),從而大大縮短機(jī)組啟動到正常運(yùn)行時間。
當(dāng)機(jī)組投入運(yùn)行后,由于固形物隨水帶入鍋爐,造成某些不溶物發(fā)生沉積,如不及時除去,沉積物會在爐內(nèi)累積,這樣一方面影響鍋爐的熱效率,另一方面也影響了鍋爐的安全進(jìn)行,嚴(yán)重時會發(fā)生鍋爐大面積的爆管。
運(yùn)行鍋爐化學(xué)清洗的目的在于除去運(yùn)行鍋爐金屬受熱面上積聚的氧化鐵垢、鈣鎂水垢、銅垢、硅酸鹽垢和油垢等。以免鍋內(nèi)沉積物過多而影響鍋爐的安全運(yùn)行。
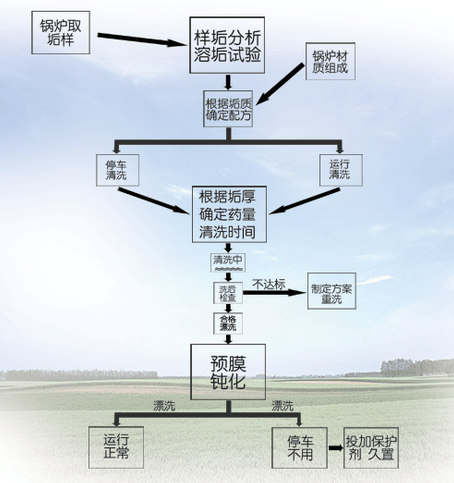
達(dá)到DL/T794《火力發(fā)電廠鍋爐化學(xué)清洗規(guī)則》(技術(shù))。HG/T2387-92《工業(yè)設(shè)備化學(xué)清洗質(zhì)量標(biāo)準(zhǔn)》。GB8978《污水綜合排放標(biāo)準(zhǔn)》等標(biāo)準(zhǔn)。
1. 清洗后的金屬表面應(yīng)清潔,基本上無殘留氧化物和焊渣,無明顯金屬粗晶析出的過洗現(xiàn)象,不應(yīng)有鍍銅現(xiàn)象。
2. 用腐蝕指示電測量的金屬平均腐蝕速度應(yīng)小于8 g/(m2•h)。腐蝕總量應(yīng)小于80g/ m2,除垢率不小于90%的合格,除垢率不小于95%為優(yōu)良。
3. 清洗后的金屬表面應(yīng)形成良好的鈍化保護(hù)膜,不應(yīng)出現(xiàn)二次銹蝕和點蝕。
4. 固定設(shè)備上的閥門、儀表等不應(yīng)受到損傷。
(1)清洗目的:
為了除去新建鍋爐在制造過程中形成的高溫氧化皮以及在存放、運(yùn)輸、安裝過程中所產(chǎn)生的腐蝕產(chǎn)物、油污、焊渣和泥沙等污染物,并形成良好的鈍化保護(hù)膜,保持熱力設(shè)備內(nèi)表面清潔,提高熱力系統(tǒng)汽水品質(zhì),防止受熱面因結(jié)垢、腐蝕引起事故,保證機(jī)組順利啟動和安全、經(jīng)濟(jì)運(yùn)行。
(2)編制依據(jù):
2.1《火力發(fā)電廠鍋爐化學(xué)清洗導(dǎo)則DL/T 794-2001》
2.2《電力基本建設(shè)熱力設(shè)備化學(xué)監(jiān)督導(dǎo)則SDJJS03-88》
2.3《火力發(fā)電廠基本建設(shè)工程啟動及驗收規(guī)范1996年版》
2.4《火電工程啟動調(diào)試工作規(guī)定1996年版》
2.5《火力發(fā)電廠停備用熱力設(shè)備防銹蝕導(dǎo)則SD223-87》
2.6《火力發(fā)電廠停備用熱力設(shè)備防銹蝕導(dǎo)則SD223-87》
2.7《火力發(fā)電廠水汽化學(xué)監(jiān)督導(dǎo)則DL/T561-95》
2.8《電力建設(shè)安全健康與環(huán)境管理工作規(guī)定(2002年版)》
2.9《火電工程調(diào)整試運(yùn)質(zhì)量及評定標(biāo)準(zhǔn)規(guī)(1996年版)》
2.10《火電機(jī)組達(dá)標(biāo)投產(chǎn)考核標(biāo)準(zhǔn)(2001年版)》
2.11設(shè)計單位、設(shè)備廠家提供的有關(guān)圖紙、資料及其它相關(guān)的技術(shù)資料,有關(guān)合同規(guī)定等。
(3)機(jī)組概況:
3.1鍋爐主要技術(shù)參數(shù)
金大地?zé)犭姽こ?3鍋爐系無錫華光鍋爐廠生產(chǎn)的UG-160/9.8-M6型循環(huán)流化床鍋爐。
3.2清洗系統(tǒng)設(shè)備部件特征參數(shù)
表一:清洗系統(tǒng)設(shè)備部件特征參數(shù)
序號 | 部件名稱 | 水容積m3 | 材 質(zhì) |
1 | 汽包 | 10.7 | 19Mn6 |
2 | 省煤器系統(tǒng) | 20G | |
3 | 水冷壁系統(tǒng) | 20G | |
4 | 臨時系統(tǒng) | 10 | 20G |
5 | 合計 | 120.5 |
(4)化學(xué)清洗范圍及清洗介質(zhì):
4.1清洗范圍
根據(jù)《火力發(fā)電廠鍋爐化學(xué)清洗導(dǎo)則》之規(guī)定及設(shè)備腐蝕狀況,并參照了國內(nèi)同類型鍋爐的清洗經(jīng)驗,確定本次化學(xué)清洗的范圍是:給水操作臺、省煤器系統(tǒng)、水冷壁系統(tǒng)、汽包、集中下水管及其有關(guān)連接管。凝結(jié)水系統(tǒng)采用水沖洗,過熱汽系統(tǒng)采用蒸汽吹洗.
4.2 清洗介質(zhì)
鑒于目前鍋爐化學(xué)清洗工藝,采用EDTA清洗具有清洗系統(tǒng)簡單,安全可靠,操作方便,容易控制,同時對被清洗部件腐蝕損害小,本次清洗選用EDTA為清洗介質(zhì)。
(5)清洗前應(yīng)具備的條件:
5.1清洗所用化學(xué)藥品已按方案中要求備齊.
5.2清洗中所需化驗儀器、藥品、記錄表格等準(zhǔn)備就緒,化驗人員經(jīng)考核合格,化驗室具備使用條件.
5.3現(xiàn)場清理工作結(jié)束,欄桿、照明等設(shè)施齊全,溝道、孔洞已采取防護(hù)措施。
5.4現(xiàn)場通訊聯(lián)絡(luò)器材已備好,能滿足清洗通訊聯(lián)絡(luò)要求。
5.5醫(yī)務(wù)部門已備好急救藥品,現(xiàn)場醫(yī)務(wù)人員到崗。
5.6搬運(yùn)藥品、執(zhí)行操作、設(shè)備檢修及現(xiàn)場指揮等人員已配齊必要的勞動防護(hù)用品,檢修人員已備好檢修所用材料及工器具。
5.7清洗組織指揮系統(tǒng)已落實,清洗各崗位工作人員已定員到崗,清洗技術(shù)負(fù)責(zé)人已向參加清洗的工作人員進(jìn)行技術(shù)交底,參加清洗的工作人員已熟悉清洗方案中的各項要求與說明.
5.8電廠制水系統(tǒng)能提供足量的除鹽水。清洗系統(tǒng)用水總量見表二 。
表二:系統(tǒng)清洗用水計劃表
序號 | 工序 | 清洗用水量 |
1 | 水沖洗 | 200-350 |
2 | 模擬試驗 | 120-250 |
3 | 清洗鈍化 | 120-250 |
4 | 合計 | 440-850 |
5.9監(jiān)視管已準(zhǔn)備完畢,系統(tǒng)連接完好,腐蝕指示片安裝在監(jiān)視管內(nèi)。監(jiān)視管安裝在水冷壁上。
5.10鍋爐已具備點火條件,與之相應(yīng)的調(diào)試項目已結(jié)束。
5.11廠用輔助蒸汽系統(tǒng)吹掃結(jié)束,具備送汽條件.
5.12清洗泵、濃堿泵等轉(zhuǎn)動機(jī)械經(jīng)試轉(zhuǎn)合格。
5.13汽包臨時水位計安裝調(diào)校合格,各水位監(jiān)視點配備了必要的通信聯(lián)絡(luò)工具。
5.14與清洗有關(guān)的電動門、調(diào)節(jié)門已調(diào)校完畢,能隨時投入使用。
5.15清洗范圍內(nèi)所涉及的設(shè)備和管道已安裝完畢,并經(jīng)水壓試驗合格,試驗壓力為清洗壓力的1.5倍.
5.16與清洗系統(tǒng)有關(guān)的設(shè)備和管道保溫工作已結(jié)束。
5.17與清洗系統(tǒng)有關(guān)的設(shè)備、閥門編號及掛牌完畢。
(6)化學(xué)清洗系統(tǒng)及安裝要求:
6.1清洗回路:疏水箱 、清洗泵、省煤器、汽包、循環(huán)母管、水冷壁、下集箱、下降管
6.2系統(tǒng)安裝要求
6.2.1鍋爐底部安裝直徑Φ159×4.5mm環(huán)型母管,水冷壁下部聯(lián)箱各間隔用直徑Φ133×4mm管子與環(huán)型母管接通。從鍋爐底部環(huán)行母管上接一Φ159×4.5 mm臨時管至疏水箱入口及一Φ159×4.5 mm臨時管至疏水泵入口母管及一Φ159×4.5 mm臨時管附近地溝,和一Φ159×4.5 mm臨時管至酸洗廢液池。
6.2.2汽包牛眼水位計暫不安裝,改裝二個臨時液位計,并標(biāo)明最高、正常、最低水位。正常水位定為汽包中心線上,高水位在中心線上150mm處,低水位在中心線下150mm處。
6.2.3在系統(tǒng)最低點處應(yīng)安裝排放管并與底排總管、臨爐加熱總管、疏水管等接至環(huán)型母管上,并延接至清洗系統(tǒng)排放總管上,便于沖洗和排放。汽包集中下降管口應(yīng)加裝開孔為Ф40mm,厚度10mm的節(jié)流孔板。
6.2.4汽包內(nèi)汽水分離裝置暫不安裝。與鍋爐本體連接的所有儀表用取樣管必須與系統(tǒng)隔離。
6.2.5利用烘爐機(jī)點火加溫。
6.2.6配藥按照疏水箱溶劑進(jìn)行配制。
6.2.7安裝臨時系統(tǒng)時,設(shè)備和管系統(tǒng)在組裝時應(yīng)對其內(nèi)部進(jìn)行檢查和清掃,使其內(nèi)部無鐵銹、泥沙、塵土、焊渣、保溫材料等污物。水平敷設(shè)的臨時管道.朝排水方向的傾斜不得小于1/200。系統(tǒng)流路上應(yīng)盡量避免出現(xiàn)U形管段、盲管段等死角區(qū)。應(yīng)按永久管道的質(zhì)量要求檢查臨時管的焊接質(zhì)量。各臨時管固定良好。
6.2.8所有閥門在安裝前必須研磨,更換格蘭填料,并進(jìn)行水壓試驗。臨時閥門的壓力等級必須高于清洗時壓力等級。閥門格蘭填料必須耐酸堿,閥桿應(yīng)涂油潤滑。
6.2.9汽包就地壓力表換成0-0.5MPa低量程壓力表。
(7)化學(xué)清洗時應(yīng)投入的系統(tǒng):
7.1煙風(fēng)系統(tǒng)
7.2爐本體系統(tǒng)
7.3燃油系統(tǒng)
7.4化學(xué)補(bǔ)給水系統(tǒng)
7.5壓縮空氣系統(tǒng)
(8)清洗工藝過程及說明:
8.1 清洗系統(tǒng)水沖洗
8.1.1 爐本體系統(tǒng)的水沖洗
疏水箱沖洗合格后,啟動清洗泵對省煤器、汽包、水冷壁進(jìn)行沖洗,至排水澄清時為合格。
8.2 堿洗操作
8.2.1準(zhǔn)備工作:打開汽包空氣門,給鍋爐上水,啟動清洗泵進(jìn)行循環(huán),邊循環(huán)邊加熱。
8.2.2加藥:當(dāng)溫度升到60℃時,依次向疏水箱內(nèi)加入定量的碳酸鈉0.5-1.5%、磷酸鈉0.5-1.5%、氫氧化鈉0.5-1.0%及潤濕劑0.03-0.05%,保持汽包高液位,溫度控制在85度左右。流程為:
疏水箱 → 清洗泵→ 省煤器→汽包→水冷壁→疏水箱
8.2.3堿洗過程:控制溫度85度左右,水位不能過高,防止溶液進(jìn)入過熱器內(nèi)。
8.2.4在堿洗時,應(yīng)每隔1小時分析堿洗液濃度。當(dāng)堿度達(dá)到平衡,則堿洗結(jié)束。打開汽包空氣門、下級箱排污門,排除廢液。
8.2.5 時間8-12小時。
8.3 EDTA清洗
8.3.1藥品配制
在疏水箱中加入計算量的除鹽水,啟動清洗泵進(jìn)行再循環(huán),加入計算量的燒堿和緩蝕劑,然后加入計算量的固體EDTA,繼續(xù)用清洗泵循環(huán),直至藥液全部溶解均勻,測定清洗液的EDTA濃度和初始PH值,最后在上藥前加入聯(lián)胺。
8.3.2 藥
藥液攪拌均勻后,用清洗泵向清洗系統(tǒng)上藥,進(jìn)藥順序為:
疏水箱→清洗泵→省煤器→汽包→水冷壁,至汽包中心線下200mm時停止上藥。
8.4 系統(tǒng)循環(huán)
當(dāng)藥液上完后,調(diào)整好汽包的水位后,利用清洗泵進(jìn)行系統(tǒng)循環(huán),鍋爐開始升溫。
8.5 系統(tǒng)清洗
8.5.1清洗工藝
EDTA 5-8% 緩蝕劑 0.5%
聯(lián)胺 1500-2000ppm 清洗PH 5.5 ~ 8.5
溫度 125±5℃(爐本體)
時間 約10~12小時
8.5.2有關(guān)說明
8.5.2.1本次清洗直接在疏水箱配藥。
8.5.2.2本次清洗加熱方式為先在疏水箱通蒸汽加熱,以鍋爐烘爐機(jī)點火維持清洗溫度。
8.5.2.3清洗時汽包保持高水位,利用底排門調(diào)節(jié)汽包水位。
8.5.2.4系統(tǒng)補(bǔ)水采用向疏水箱的補(bǔ)水方式。
8.5.2.5汽包壓力可作為溫度監(jiān)測的輔助手段。
8.5.2.6清洗階段應(yīng)考慮補(bǔ)加藥措施。
8.6 鈍化
當(dāng)清洗液PH≥8.0時,可以認(rèn)為進(jìn)入鈍化階段。
PH 8.0 ~ 9.0
溫度 105±5℃(爐本體)
8.7 排液
鈍化結(jié)束后,停爐降溫,當(dāng)溫度降至90℃以下時,將廢液排至酸洗廢液池暫存起來,用臨時泵噴灑至煤廠,考慮每天20噸。EDTA的成分為C、H、O、N燃燒后生成二氧化碳、水、二氧化氮,不會對環(huán)境造成污染。
8.8清洗階段化學(xué)監(jiān)督項目一覽表
測定項目 | 取樣間隔 |
總EDTA | 2h |
剩余EDTA | 30min |
PH | 30min |
溫度 | 30min |
Fe2+、Fe3+ | 1h |
(9)清洗組織機(jī)構(gòu)及職責(zé)分工:
化學(xué)清洗臨時系統(tǒng)多,由多專業(yè)配合完成,因此必須成立清洗領(lǐng)導(dǎo)小組,負(fù)責(zé)指揮協(xié)調(diào)整個清洗工作。
9.1.職責(zé)分工
安裝單位:
1)負(fù)責(zé)組織實施化學(xué)清洗工作;
2)臨時設(shè)施的制作、安裝和系統(tǒng)恢復(fù)工作;
3)設(shè)備與系統(tǒng)的維護(hù)、檢修和消缺;
4)清洗階段臨時系統(tǒng)的操作;
調(diào)試單位:
1)方案的編制、技術(shù)指導(dǎo);
2)清洗前的系統(tǒng)檢查、技術(shù)交底、模擬試驗工作;
3)清洗過程中的技術(shù)指導(dǎo)以及清洗效果檢查與測定;
4)清洗后參加清洗效果評定提出清洗總結(jié)報告。
電廠:
1)參與清洗技術(shù)指導(dǎo)與監(jiān)督;
2)清洗階段正式系統(tǒng)的操作;
3)清洗化驗準(zhǔn)備及分析工作。
(10)清洗后的檢查與評定:
10.1.清洗結(jié)束后,迅速取下監(jiān)視管,鑒定清洗效果;
10.2.清洗結(jié)束后,迅速取出腐蝕指示片并測定其腐蝕速率;
10.3.清洗結(jié)束后,根據(jù)要求迅速割取管樣(注:割取長度不小于200mm,不得使用火焊割?。?,鑒定清洗效果;
10.4.檢查汽包、下聯(lián)箱內(nèi)表面的清潔程度,并清理沉積物;
10.5.化學(xué)清洗應(yīng)達(dá)到如下標(biāo)準(zhǔn):
10.5.1.被清洗金屬表面清潔,無殘留氧化物;
10.5.2.被清洗金屬表面無明顯粗晶粒析出和點蝕,并形成保護(hù)膜;
10.5.3.腐蝕指示片平均腐蝕速率≤8g/(m2.h);腐蝕指示片平均腐蝕總量≤80g/m2;
10.6.根據(jù)上述各項檢查結(jié)果進(jìn)行總評。
(11)藥品用量估算:
表四:清洗藥品一覽表
序號 | 名稱 | 分子式 | 純度 | 數(shù)量 |
1 | 燒堿 | NaOH | 40% | 8噸 |
2 | EDTA | 99% | 6噸 | |
3 | 水合聯(lián)胺 | N2H4H2O | 80% | 600公斤 |
4 | 緩蝕劑 | XJ-225 | 600公斤 | |
5 | 除油劑 | XJ-5 | 1000公斤 | |
6 | 消泡劑 | XJf-02 | 200公斤 |
(12)安全措施:
12.1清洗期間除各單位專職安全員負(fù)責(zé)日常安全工作外,清洗現(xiàn)場還應(yīng)專設(shè)清洗安全員,具體負(fù)責(zé)清洗現(xiàn)場的安全及安全檢查工作。
12.2鍋爐化學(xué)清洗前應(yīng)組織參加清洗的工作人員學(xué)習(xí)本方案中有關(guān)部分,明確各自分工,熟悉清洗工藝過程和清洗系統(tǒng),熟練地掌握操作技術(shù)和安全知識。
12.3現(xiàn)場還必須備有消防設(shè)備。掛貼“注意安全”、“嚴(yán)禁明火”、“請勿靠近”、“有毒危險”“防止?fàn)C傷”等標(biāo)牌,并做好安全宣傳工作.
12.4清洗現(xiàn)場、取樣點附近、臨時化驗室,必須設(shè)水源,用軟管連接,以備泄漏時沖洗。
12.5清洗前.所到化學(xué)藥品必須妥善保管,以防變質(zhì)和發(fā)生意外事故。
12.6清洗現(xiàn)場應(yīng)有充足的照明設(shè)施,對影響人身安全的扶梯、孔洞、溝道,未拆除的腳手架等應(yīng)妥善處理。
12.7清洗時.系統(tǒng)出現(xiàn)故障無法循環(huán)時,應(yīng)關(guān)閉有關(guān)閥門,系統(tǒng)轉(zhuǎn)入浸泡。待處理后,再進(jìn)行循環(huán)清洗?,F(xiàn)場要求有檢修人員值班,隨時檢修清洗設(shè)備的故障。開關(guān)閥門不得用力過猛以防閥門掉芯。
12.8整個化學(xué)清洗過程要嚴(yán)格控制汽包上下壁溫差小于50℃。
12.9參加配加藥品人員應(yīng)穿防護(hù)工作服,帶防毒口罩、橡膠手套、膠布圍裙、防護(hù)眼鏡、穿長筒靴,褲腳應(yīng)放在靴外。
12.10現(xiàn)場應(yīng)有醫(yī)務(wù)人員值班,并備有 2%和 0.5%的 NaHCO3溶液及2%硼酸溶液。若酸液濺到皮膚上應(yīng)立即用清水沖洗再用2%的NaHCO3溶液清洗。若酸液濺入眼睛內(nèi)應(yīng)立即用大量清水沖洗,再用 0.5%的 NaHCO3溶液清洗,必要時送醫(yī)院治療,若堿液濺到眼睛內(nèi)和皮膚上時應(yīng)迅速用大量清水沖洗,再用2%稀硼酸溶液清洗。必要時送醫(yī)院治療.
- ● 本網(wǎng)站致力于提供正確、完整的技術(shù)資料,但不保證信息的正確性和完整性,且不對因信息的不正確或遺漏導(dǎo)致的任何損失或損害承擔(dān)責(zé)任。
- ● 本站所提供的技術(shù)文章,僅供參考,如自行使用本站資料發(fā)生偏差,本站概不負(fù)責(zé),亦不負(fù)任何法律責(zé)任。
- ● 如需技術(shù)支持,請致電我公司技術(shù)與銷售咨詢熱線:020-85690958。